STRUCTURAL INTEGRITY ASSESSMENT
(FITNESS FOR SERVICE)
FRACTURE MECHANICS
Araújo Engenharia performs the criticality analysis to evaluate cracks or discontinuities, and calculation of the remaining service life in accordance with API-579 (Part 9) and BS-7910 Standards.
Different types of analysis are offered according to your demand, among them: Linear Elastic Fracture Mechanics (MFLE), Elasto-Plastic Fracture Mechanics (MFEP) and crack propagation analysis.
Software developed in Python by the team of engineers at Araújo carry out propagation calculations, create FAD graphs (Failure Assessment Diagram) and automate the analysis process of multiple defects.
Stress analysis can also be used in the evaluation of discontinuities for numerical calculation of the stress intensifier factor (KI) or calculation of the J integral.
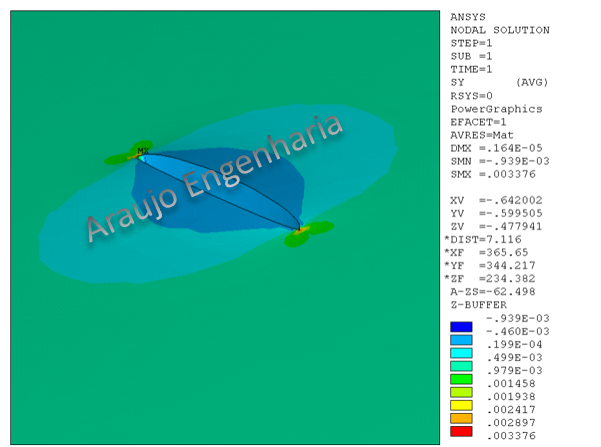
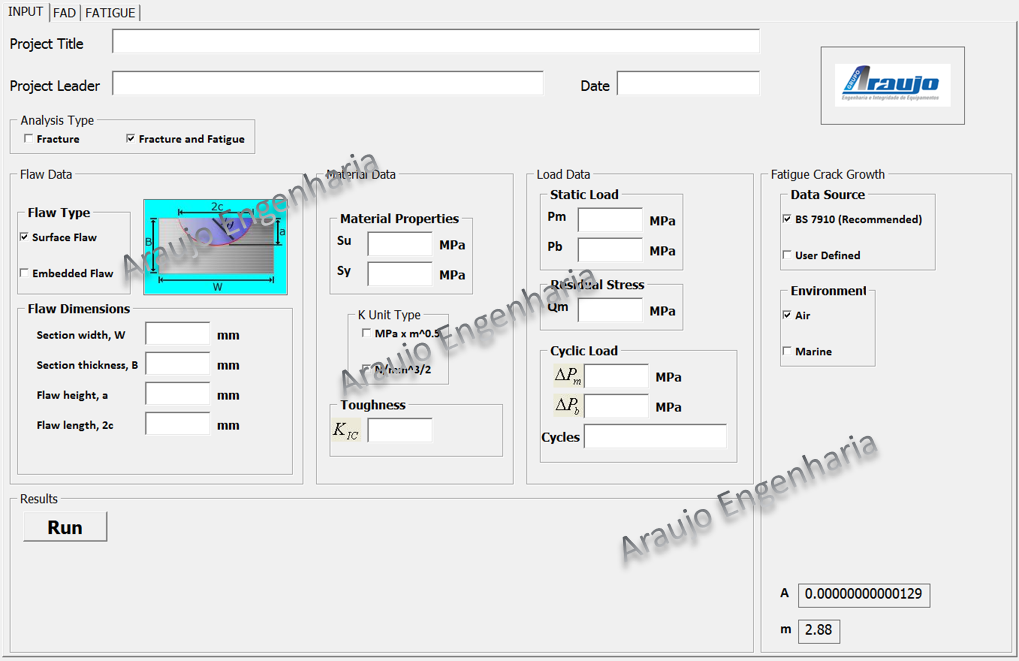
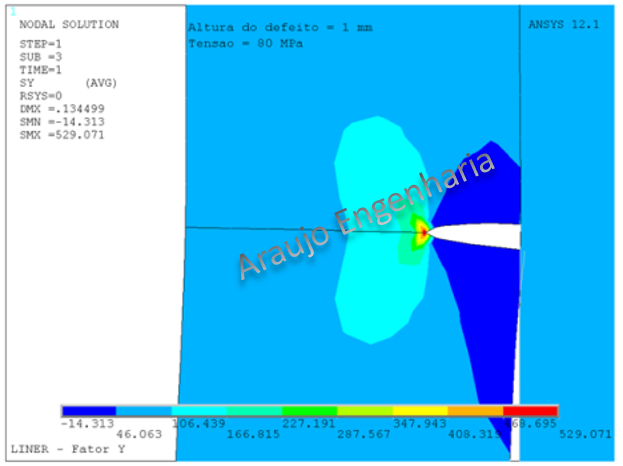
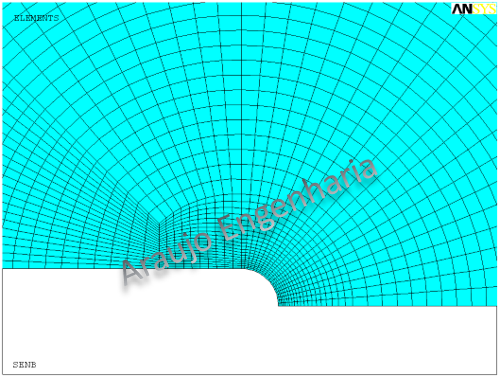
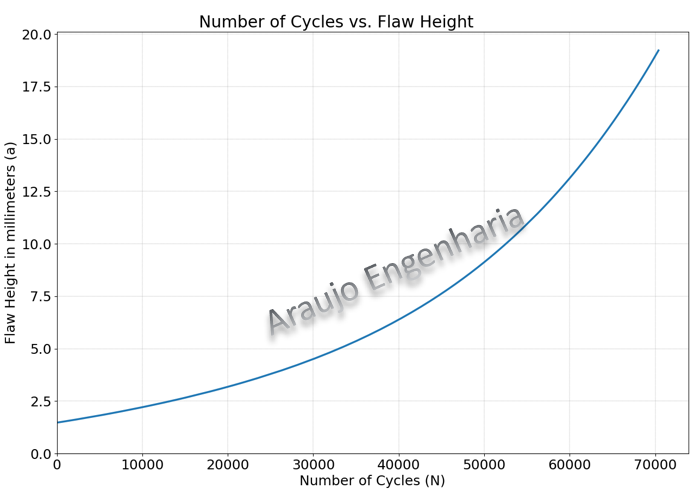
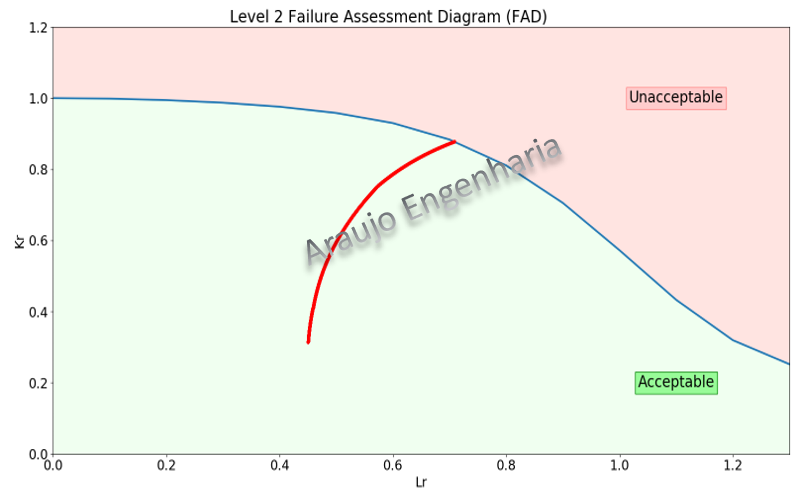
AREAS OF EXPERTISE
Analysis of Resistance
to Fragile Fracture
Analysis of Local and
Generalized Thickness Loss
Corrosion Analysis
by Pites
Hydrogen Damage
Analysis
Analysis of Shape
Deviations
Crack Analysis by
Fracture Mechanics
High Temperature and
Creep Damage Analysis
Fire Damage
Analysis
Kneading Damage
Analysis
Technical Analysis
of Laminations
Fatigue Analysis (domain
of time and frequency)
Tubes Flexibility
Analysis
Stress Analysis
conf. ASME VIII Div II
Stress Analysis of
Metallic Structures
3D SCAN
The figures below present an example of Level 3 analysis (API-579, Part 5) of localized thickness loss based on point clouds obtained by 3D scanning.
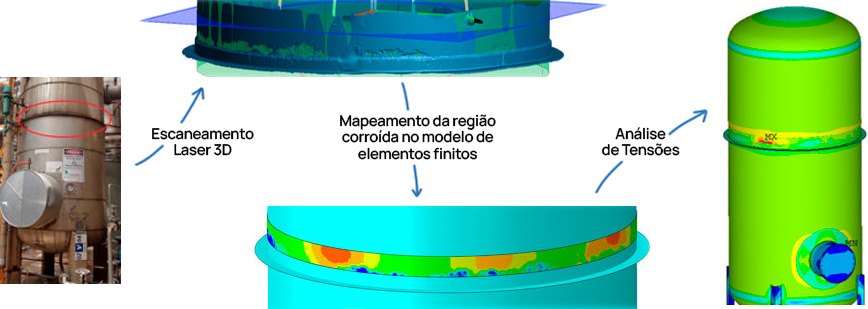
3D SCAN + STRESS ANALYSIS = SOLUTION
Araújo is the only Brazilian company that provides the “complete package” of 3D scanning solutions together with stress analysis for your company.
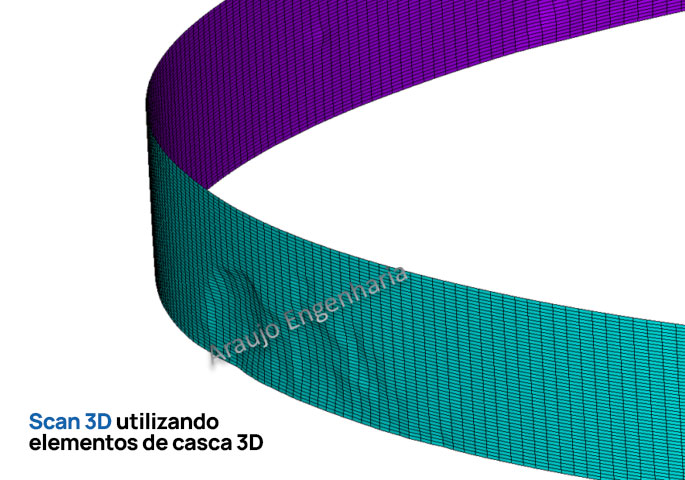
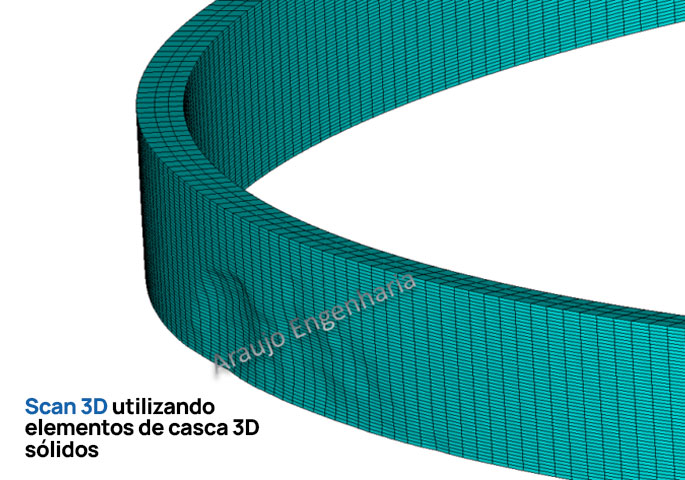
CREEP ANALYSIS
Among the finite element thermal analyzes carried out by Araújo Engenharia, the creep analysis stands out in accordance with Part-10 of API-579 Assessment Of Components Operating In The CreepRange. Araújo implemented the creep equations presented in API-579 as a subroutine in the ANSYS software (usercreep.f) for the calculation of stress relaxation and creep damage.
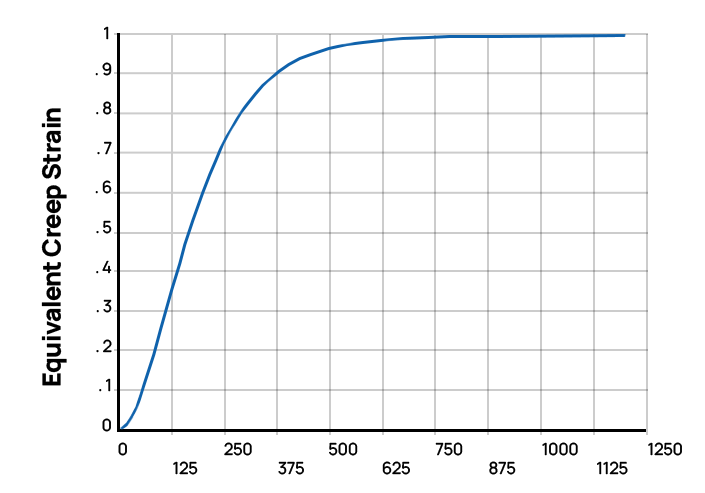